Ob in der Industrie, Logistik oder Produktion – leistungsfähige Förderschläuche sind ein entscheidender Faktor für einen störungsfreien Materialfluss. Doch nicht jede Ausstattung passt zu jedem Einsatzzweck. Die Wahl der richtigen Komponenten beeinflusst nicht nur die Effizienz, sondern auch die Sicherheit und die Betriebskosten. Unternehmen, die hier unüberlegt entscheiden, riskieren hohe Folgekosten durch Materialverschleiß, unerwartete Stillstände oder ineffiziente Prozesse. Wer wirtschaftlich arbeiten will, sollte die wichtigsten Auswahlkriterien kennen und gezielt in die passende Ausstattung investieren.
Produktivität beginnt mit der richtigen Ausstattung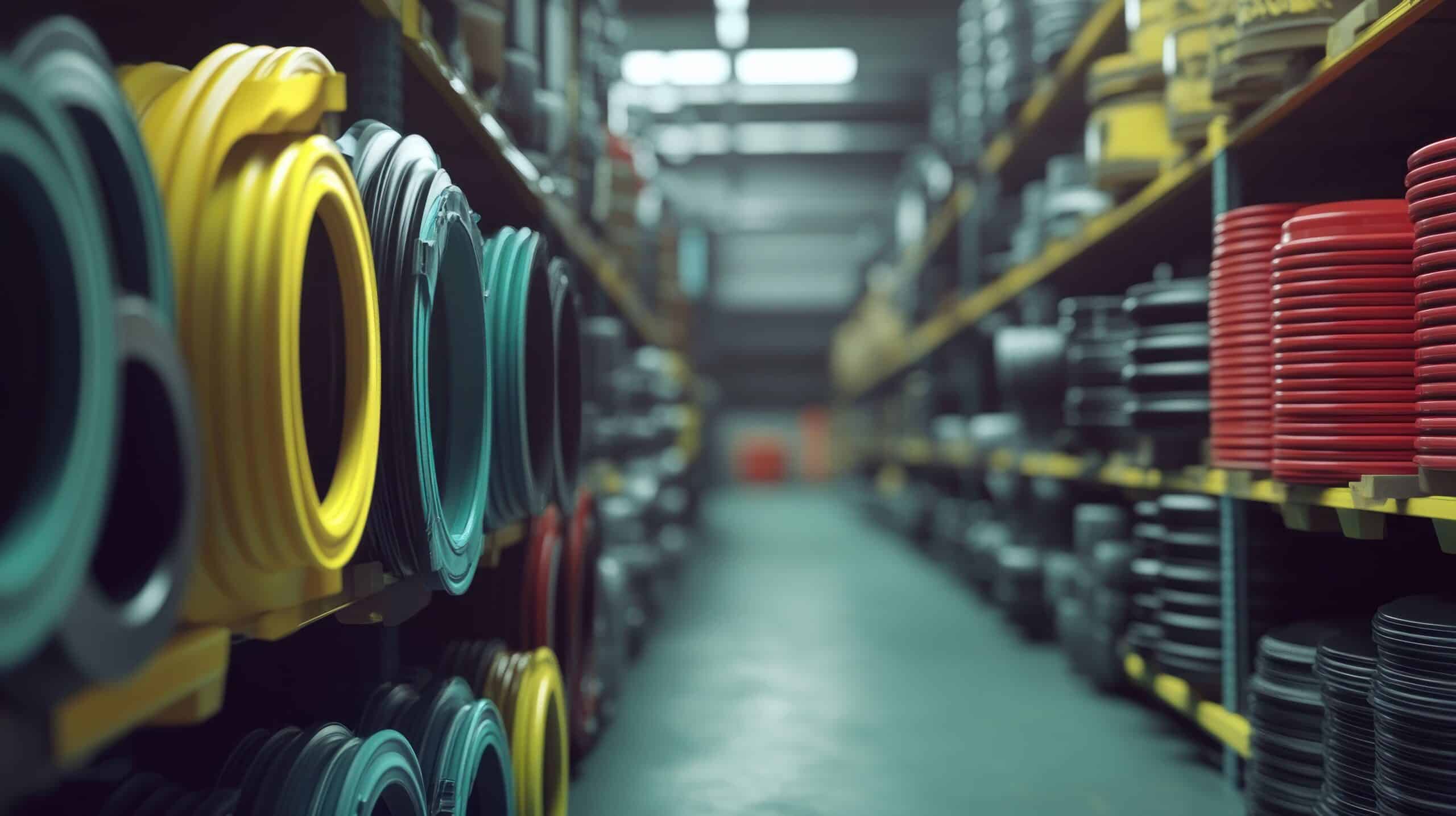
Jeder industrielle Prozess ist nur so effizient wie seine schwächste Komponente. Ein optimal geplanter Arbeitsablauf kann ins Stocken geraten, wenn ein einzelnes Element in der Kette nicht leistungsfähig genug ist oder nicht zu den spezifischen Anforderungen passt. Eine unzureichende Ausstattung führt nicht nur zu Verzögerungen, sondern kann die gesamte Produktionskette beeinträchtigen. Ein ineffizient geplanter Materialfluss führt zu Engpässen und Verzögerungen – der richtige Förderschlauch sorgt hingegen für eine gleichmäßige und verlässliche Beförderung von Stoffen.
Ein Beispiel: In einer automatisierten Fertigungsanlage kann ein ungeeignetes Fördersystem die Durchflussmenge begrenzen. Statt einer konstanten und gleichmäßigen Beförderung kommt es zu Staus oder gar Unterbrechungen. Maschinen stehen still, Personal muss manuell nachhelfen – das verursacht nicht nur höhere Kosten, sondern auch unproduktive Wartezeiten.
Auf der anderen Seite zeigt sich in gut aufeinander abgestimmten Produktionslinien, dass durch die richtige Wahl der Komponenten Effizienz und Leistung spürbar gesteigert werden. Unternehmen, die in hochwertige und bedarfsgerechte Lösungen investieren, profitieren langfristig von weniger Wartungsaufwand, reduzierten Stillstandszeiten und einem optimierten Materialfluss. Das Resultat ist eine höhere Wettbewerbsfähigkeit in einem zunehmend anspruchsvollen Markt.
Wie sich eine falsche Wahl auf den Betrieb auswirkt
Viele Unternehmen unterschätzen die Auswirkungen, die eine unpassende Ausstattung auf den Betrieb haben kann. Auf den ersten Blick mag eine kostengünstige oder universelle Lösung attraktiv erscheinen – doch die langfristigen Konsequenzen sind oft gravierend.
Erhöhter Verschleiß und häufigere Ausfälle
Komponenten, die nicht speziell für die jeweilige Anwendung ausgelegt sind, nutzen sich schneller ab. Dies kann durch Materialermüdung, Abrieb oder chemische Reaktionen geschehen. Ein ständiger Austausch verursacht hohe Ersatzteil- und Wartungskosten und führt zu Produktionsausfällen.
Unnötige Kosten durch Ineffizienz
Eine nicht optimal dimensionierte Ausstattung kann zu übermäßigem Energieverbrauch und höherem Ressourcenbedarf führen. Beispielsweise müssen Maschinen mit größerem Druck oder höheren Drehzahlen arbeiten, um den Materialfluss auszugleichen – das schlägt sich in steigenden Betriebskosten nieder.
Leistungseinbußen und Kapazitätsengpässe
Wenn eine Komponente nicht auf die Anforderungen abgestimmt ist, kommt es zwangsläufig zu Einbußen in der Produktionskapazität. Ein zu kleiner Durchmesser kann beispielsweise die Fördermenge begrenzen oder zu Staus führen. Das bedeutet geringere Stückzahlen, Verzögerungen in der Lieferkette und mögliche Vertragsstrafen durch verspätete Aufträge.
Sicherheitsrisiken für Mitarbeiter und Maschinen
Neben wirtschaftlichen Aspekten spielt auch die Arbeitssicherheit eine entscheidende Rolle. Komponenten, die nicht für hohe Belastungen oder aggressive Stoffe ausgelegt sind, können Leckagen, Defekte oder sogar Unfälle verursachen. Das gefährdet nicht nur Maschinen, sondern auch das Personal.
Ein durchdachter Auswahlprozess hilft, solche Probleme zu vermeiden und die Betriebssicherheit nachhaltig zu gewährleisten.
Kriterien für eine optimale Ausstattung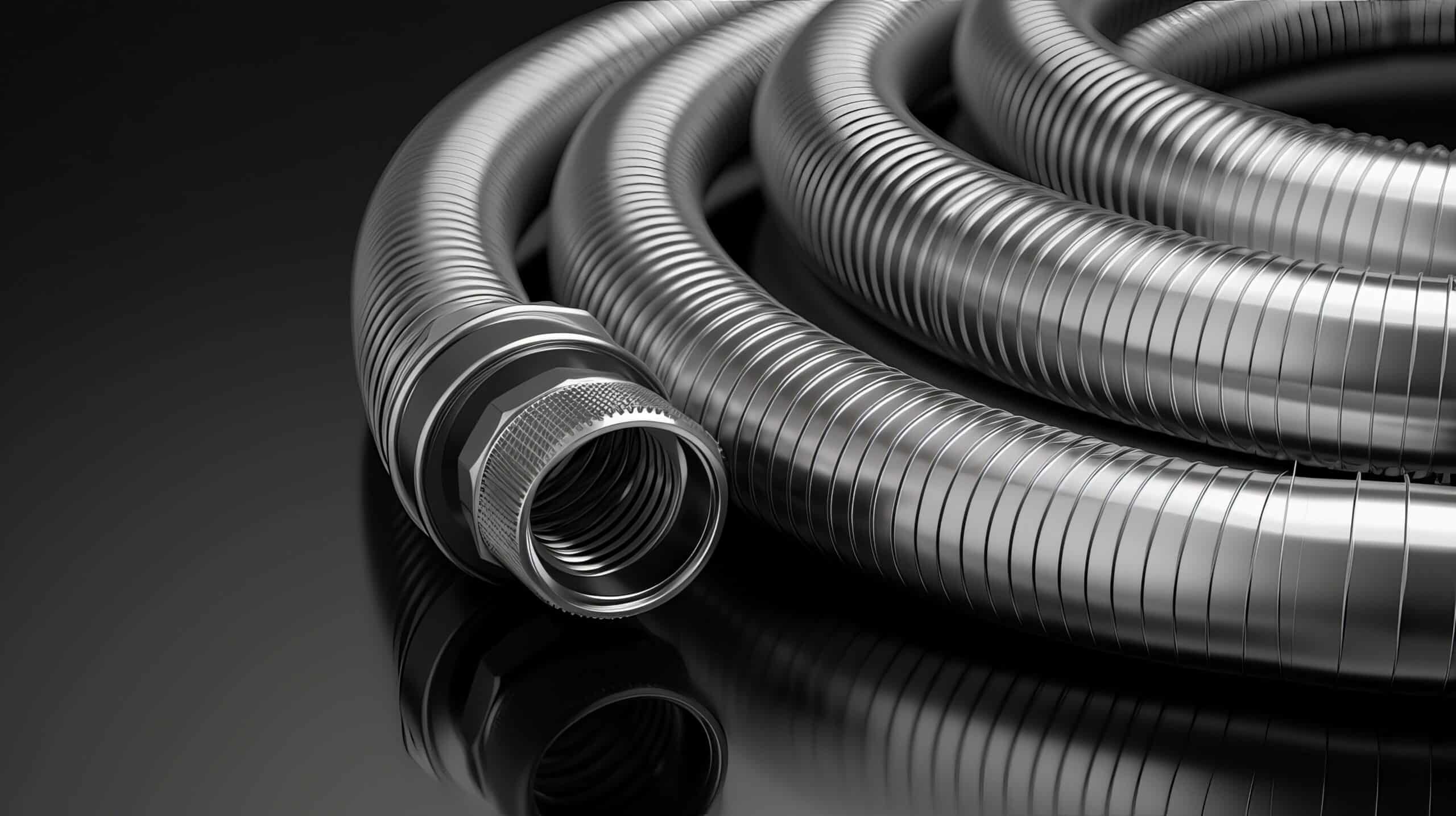
Wer seine Produktivität steigern will, sollte bereits bei der Auswahl die entscheidenden Kriterien im Blick haben. Die Anforderungen sind von Branche zu Branche unterschiedlich – doch einige zentrale Faktoren sind immer relevant:
Materialbeständigkeit
Das Material muss den Umgebungsbedingungen standhalten. Hohe Temperaturen, aggressive Chemikalien oder mechanischer Abrieb stellen unterschiedliche Anforderungen an die Ausstattung. Ein falsches Material kann spröde werden, reißen oder mit transportierten Substanzen reagieren.
Durchmesser und Flexibilität
Die Dimensionierung ist entscheidend für die Leistungsfähigkeit. Ein zu kleiner Durchmesser kann zu Staus und Druckverlusten führen, während zu große Dimensionen unnötig Materialkosten verursachen. Auch die Flexibilität ist wichtig: In beengten Produktionsstätten oder bei beweglichen Systemen sollte die Ausstattung flexibel genug sein, um sich den Gegebenheiten anzupassen.
Langlebigkeit und Wartungsfreundlichkeit
Investitionen in langlebige Komponenten amortisieren sich schnell. Hochwertige Materialien und durchdachte Konstruktionen reduzieren Verschleiß und minimieren Ausfallzeiten. Gleichzeitig sollte die Ausstattung wartungsfreundlich sein: Schnellwechsel-Systeme oder leicht zugängliche Anschlussstellen erleichtern den Austausch und reduzieren Stillstandzeiten.
Energieeffizienz
Die Energieeffizienz von Produktionsprozessen gewinnt zunehmend an Bedeutung. Eine durchdachte Ausstattung reduziert den Energieverbrauch, indem sie Reibungsverluste minimiert oder durch leichtere Materialien weniger Widerstand erzeugt. In Zeiten steigender Energiekosten ist das ein entscheidender Wettbewerbsvorteil.
Optimierungsmöglichkeiten für den Betrieb
Selbst die beste Ausstattung entfaltet ihr volles Potenzial nur, wenn sie richtig eingesetzt und gepflegt wird. Unternehmen können durch gezielte Maßnahmen noch mehr Effizienz aus ihren bestehenden Systemen herausholen:
Regelmäßige Wartung und Inspektion
Verschleißteile sollten frühzeitig überprüft und ausgetauscht werden, bevor es zu einem Ausfall kommt. Moderne Sensorik kann den Zustand der Komponenten überwachen und rechtzeitig Warnsignale senden.
Automatisierung und Digitalisierung
Durch den Einsatz von digitalen Steuerungssystemen lassen sich Arbeitsprozesse besser kontrollieren. Automatische Anpassungen an die Durchflussmenge oder vorausschauende Wartung können Probleme erkennen, bevor sie auftreten.
Schulung des Personals
Mitarbeiter, die die Funktionsweise der Anlagen genau verstehen, können schneller auf Störungen reagieren und Wartungsmaßnahmen gezielt durchführen. Gut geschultes Personal trägt maßgeblich zur Effizienzsteigerung bei.
Die richtige Wahl zahlt sich aus
Die Wahl der passenden Ausstattung ist keine Nebensache – sie entscheidet über die Leistungsfähigkeit eines Unternehmens. Eine durchdachte Auswahl und regelmäßige Optimierung sorgen für reibungslose Abläufe, reduzierte Kosten und höhere Sicherheit. Wer gezielt in hochwertige und effiziente Lösungen investiert, profitiert langfristig von mehr Produktivität und geringeren Betriebsausgaben. Ein wirtschaftlicher Betrieb beginnt mit einer fundierten Entscheidung.
Bildnachweis: putri syakilla, Collection, Maksym/ Adobe Stock